THE PERMANENT MATERIAL IN THE LOOP
Steel at the end of each life cycle allows 100% recycling – steel scrap can be infinitely be recycled – strongly promoting a circular economy. By-products generated during the steel production process, like dusts/sludges and slags can be recycled as well, but require dedicated solutions to achieve circularity, also a cross industry approach.
ZINC EXTRACTION PROCESS
The new Zinc Extraction Process, the complete dust-recycling solution for the recovery of zinc and iron, is a zero-waste recycling solution for dust from steelmaking. In the first step, the dust is treated in oxidizing conditions in a short drum furnace to vaporize halides and heavy metal components. In the second step, the clinkered dust is melted and treated in reducing conditions in an EAF, where a high-quality zinc oxide (ZnO) and the metallic fraction are recovered for reuse in steel making, along with a mineral fraction that can be used in the construction industry. The ZnO produced requires no further washing and can be used directly in the primary zinc industry. Development and prototype tests have been successfully completed, and the first industrial reference is planned.
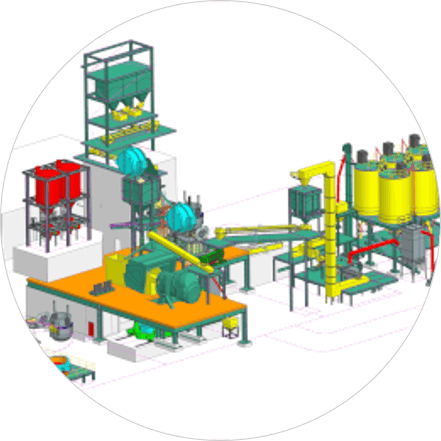
Slag Valorization
Steelmaking slag amount to more than 13 percent of total steel plant output and contains valuable materials like iron oxides and minerals. In many plants, this valuable byproduct is still being landfilled. In order to enable a circular economy with increased byproduct utilization, Primetals Technologies has developed a process for valorizing steelmaking slag. The slag is treated in an electric arc furnace under reducing conditions so that the metal fraction (mainly iron) can be recovered, and the mineral fraction is modified to allow its use in the construction industry: for example, as a cement clinker substitute. Depending on the phosphorus content of the raw materials used, the recovered metal often needs further dephosphorization in a separate treatment stand before it can be reused in steelmaking. The industrial feasibility of this patented process has been successfully proven on both the lab and pilot levels. Now that there are limited landfilling options, increasing raw material prices, and more pressure to reduce CO2 emissions, the business case for this kind of zero-waste byproduct recycling process is promising. We’re ready with our expertise and solutions to save your resources and convert steelmaking slag into valuable products and future earnings.
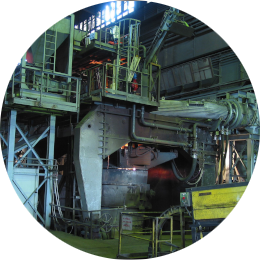