Smart sensors and automatic functions
A wide range of intelligent solutions for transparent, reliable, and safe operation
To ensure that each production facility can play its part in the digital plant, it has to fulfill certain preconditions, meaning that it must have the highest possible degree of automation combined with high availability. Smart sensors, monitoring tools, and robotic applications make a significant contribution here by leading to greater transparency of all production steps and enabling the systems to operate automatically.
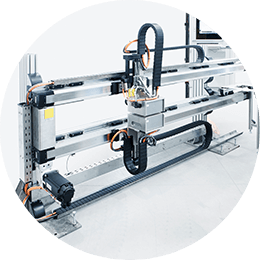
Pave the way for process optimization
Intelligent sensors provide essential information about the processes taking place and the actual condition of the production facilities
They directly measure physical values or use preexisting data to calculate additional information. Measuring tools for plant conditions enable predictive maintenance, and sensors for processes and products provide detailed information on various parameters during production.
The information from smart sensors is the enabler for the implementation of process models and advanced automatic functions. It makes it easier to improve those processes that could yield higher performance.
Here you find more information on our range of smart sensors
Name | Short Description |
---|---|
Automatic Thermocouple Checker | Automatic sensor test for breakout prediction system for continuous casting |
Lomas | Gas analysis system for very hot corrosive and dust-loaded process gases |
Mold Checker | 3D measurement for the inner shape of continuous casting molds |
OsciChecker | Portable device for mold oscillation measurement in continuous casting machines |
Position Transducer | Position measurement of rolling mill hydraulic capsule |
Taper Checker | Measurement for taper adjustment for slab casters |
VD Contact-free Temperature Measurement | Contact-free temperature measurement under vacuum for VD and VOD plants |
Make Your Processes Transparent
Process monitoring is essential for safe, reliable, efficient operation and product quality
For process optimization and quality purposes, current material and process parameters must be available without interruption during the entire production process. Monitoring solutions permanently collect information from integrated sensor systems or measuring devices, e.g., cameras or microphones, and calculate relevant parameters in real time. With continuous visualization and evaluation of the results, our monitoring tools provide comprehensive support for the operator. The results can easily verify and detect production, product quality, or equipment deviations. Overall, the application of monitoring systems leads to better transparency about the processes and thus ensures stable production and high product quality.
Here you find more information on our range of monitoring solutions
Name | Short Description |
---|---|
Bag Cleaning Monitor | Acoustic monitoring of pulse jet bag filter plants |
Discharge Monitor | Acoustic monitoring of truck or wagon discharging |
EdgeMon | Inspection of side-trimmed strip edge surface for steel pickling and processing lines and aluminum rolling |
Equipment Position Monitor | Reliable identification and tracking of metallurgical equipment throughout the steel plant |
Grain Size Monitor | Acoustic measurement of material grain size on conveyor belts |
Leakage Monitor | Leakage detection system for water cooling circuits |
Material Type Monitor | Automatic identification of the type of material on conveyor belts |
OsciMon | Online monitoring of mold oscillation in continuous casting machines |
PropertyMon | Inline measurement of steel strip properties |
ShapeMon Billet Bloom | Measuring solution for weight and geometry for billets and blooms |
ShapeMon HSM | Camber and centerline measurement for hot mills, plate mills, and ESP |
SlagMon | Reliable slag detection for optimized tapping |
TorqueMon | Inline measurement of roll spindle torque for rolling mills |
Focus on the Essential Tasks with Robotic Solutions
Fully automated mechatronics solutions and assistance systems support repetitive, labor-intensive, and dangerous work
These technologies allow your staff to focus on those tasks where human interaction is indispensable.
Robotic systems were developed primarily to improve job safety and quality of measurements under harsh conditions in the iron and steel industry. Our robots are excellently suited to the variety of work activities necessary in production.
Automatic procedures increase process reliability, job safety, flexibility, productivity, and product quality. Each aspect of the production chain can be monitored in the control room, where operating personnel are safe from hazards.
Here you find more information on automatic functions and robotic solutions
Name | Short Description |
---|---|
BOF Tapping Expert | Safe tapping for all types of steelmaking converters - LD (BOF), AOD and KOBM |
LiquiRob for Casting | Robotic solution for continuous casting machines |
LiquiRob for Steelmaking | Robotic solution for EAF, BOF, ladle furnace, VD |
Sinter Raw Mix Analyzer | Robotic solution for sinter plants |