PLATE MILL — POWER MEETS PRECISION
Plate Mills are quite literally the most powerful metal-working tools on earth, but they are precision tools too.
Precise control of dimensions is critical, and so is imparting mechanical properties to the rolled product. The plate rolling process affords great flexibility in terms of how mechanical properties are achieved, through a combination of alloying, working the material, and accelerated cooling processes. Accurate microstructural control starts with expert process knowledge. Primetals Technologies has bundled this knowledge into its process equipment and is able to work closely with our customers to develop the most cost-effective solution for their specific needs.
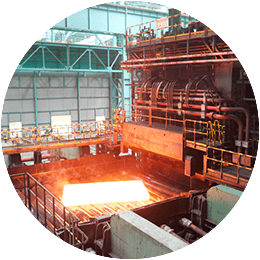
PLATE MILLS – DELIVERING METALLURGICAL PRECISION
Primetals Technologies has successfully completed over 70 Plate Mill projects since 2000, including new full lines, mechatronic packages and major modernizations.
Our plate equipment portfolio consists of:
- Plate Mill (Roughing Mill, Finishing Mill, with Edger option)
- Primary and Mill Stand Descaling Systems
- Pre-levellers
- MULPIC® Accelerated Cooling & Direct Quenching
- Hot Plate Levellers
- Hot Divide Shears
- Cooling Beds
- Double Side Trimming Shears
- Slitting Shears
- Dividing Shears
- Cold Levellers, specifically designed for production of thin and thick high-strength products
- Plate Heat Treatment Lines (Normalizing, Quench & Temper)
Bottom Mounted Long Stroke HAGC
Plate Mill stands equipped with this feature benefit from active passline adjustment, reducing turn-up and turn-down rolling defects as well as lowering maintenance time and cost through the elimination of fixed and stepped packers. Industry thickness quality requirements are also exceeded.
SmartCrown® Work Roll Shifting
As well as increased plate profile accuracy and improved plate flatness, reductions per pass are increased leading to higher productivity, particularly for thin plates.
Direct Application of Levelling Load
The Thin Gauge High Strength Leveller and Power Leveller, specialized for thin and thick high strength plate respectively, utilize the direct application of levelling and bending load through six or more HAGC cylinders with internal position transducers. This allows the most precise control of the plate and leveller cassette deformation, leading to the highest quality, flat, high strength plates.
Primetals Technologies has built up a wealth of expertise in the Thermo-mechanical Controlled Processing (TMCP) of steel plates. Central to this process is the accelerated cooling of the plates after rolling.
Accelerated Plate Cooling
MULPIC® (Multi Purpose Interrupted Cooling) is the world-leading plate cooling technology. Its large flow control range (20:1) allows for both the Direct Quenching (DQ) of Abrasion Resistant and High Strength Steels and the lower cooling rates needed for high carbon or lower strength steels. High cooling rates lead to alloy savings on critical products such as Pipeline Steels, as well as improved toughness and weldability. The cooling header design, coupled with actuators to control the flow across the width leads to reduced residual stress and improved flatness compared to conventional spray and laminar systems.
MULPIC®’s flexible, modular design allows it to be integrated with existing cooling systems to form hybrid systems. This enables higher cooling rates, improved flatness and an expanded product range with minimal capital expenditure. Such systems have allowed the production of up to 500 Brinell Hardness abrasion resistant steel plates online as well as providing significant alloy savings on micro-alloyed steel plates.
With the increasing importance of steel production’s impact on the environment, many of MULPIC®’s unique technological design features have been optimized to support sustainably greener steel production.
Want to know more? Go to Lifecycle Services & Integrated Plants & Solutions
COMPLETE AUTOMATION AND PROCESS CONTROL FOR PLATE MILLS
Plant productivity and product quality are substantially depending on the quality of plant automation, process control, and available process optimization functions. Primetals Technologies provides standardized high-performance automation systems seamlessly integrating:
- Digitalization packages (e.g. TPO, MAT, Condition Monitoring, Intelligent Sensors)
- Production management systems (Level 3)
- Physical models combined with artificial intelligence (Level 2)
- Automation solutions including advanced technological controls (Level 1)
For existing installations, optimization packages are available as stand-alone solutions to improve production efficiency and strip quality.
Throughput maximization with:
- Dynamic Batching and advanced Interleaving for thermo-mechanical rolling
- Mill Pacing including Cooling beds charging optimization
Excellent strip quality with:
- Contour and Flatness Optimizer
- Model predicted roll alignment control to minimize camber (MRAC)
- Wedge and Camber Expert
- De-Tappering to improve Head/Tail thickness tolarances
Our solutions provide:
- Process Automation Twin to safely develop new materials and to optimize rolling schedules
- Central Operation Cockpit to support mill operations (centralized pulpit)
- Software architecture open for customers own future developments
- Modular structure for step-by-step modernizations
TECHNOLOGY AND MODERNIZATION PACKAGES
Get striking results with incremental investments
Name | Short Description |
---|
Name | Short Description |
---|
Name | Short Description |
---|
Name | Short Description |
---|---|
Encopanels | Heat retention system for Hot Strip Mills |
Contour and Flatness Optimizer | Measuring and optimization of strip contour and flatness |
Microstructure Monitor | Determination of material properties for Hot Strip and Plate Mills |
Mill Stabilizing Device (MSD) | Proven solution for stable operation in challenging rolling conditions |
Online Roll Profiler (ORP) | Online work-roll grinding for work-roll wear treatment |
TorqueMon | Inline measurement of roll spindle torque for rolling mills |
ShapeMon HSM | Camber and centerline measurement for hot mills, plate mills, and ESP |
Integrated Solenoid Valve (ISV) Spray System | ISV Roll coolant spray bars for hot and cold rolling mill strip flatness control |
Width-Gauge Stereo Camera | Non-contact stereoscopic camera width-gauging systems for Hot Strip Mills |
Position Transducer | Position measurement of rolling mill hydraulic capsule |
MULPIC® Flow Control | Flow control valves and automation solution for plate and steckel mill |
MULPIC® Process Control | Level 2 and cooling model for plate and steckel mill |
MULPIC® Hybrid Cooling | Flexible hybrid cooling solution for plate and steckel mill |
Strip Cooling Technology | Innovative and tailor-made strip cooling solution |
Name | Short Description |
---|
Name | Short Description |
---|
Reference Story: Product mix extended to include high-strength structural steels
Customer
Baosteel Zhanjiang Iron and Steel Co., Ltd., PR China
Type of plant
Heavy Plate Mill
Our solution
Primetals Technologies MULPIC® accelerated cooling technology enables the production of plates with a uniform microstructure along the length and width of the plate. Read more
What the customer says
“The product mix is dramatically extended by the application of the MULPIC® in Zhanjiang Heavy Plate Mill Plant. Using the MULPIC®, we successfully produced TMCP API steel and high-strength structural steel.”
Mr. Chen, Baosteel.