CONVERTER CARBON STEELMAKING — BOOST YOUR COMPETITIVE EDGE WITH FULL-LINE SOLUTIONS FROM THE PROCESS INVENTOR
The demands placed on product quality, plant productivity and availability are on the rise. LD (BOF) plants from Primetals Technologies lead the steelmaking sector in terms of reliability and economy.
When engineers in the early 1950s were looking for alternatives to the Siemens-Martin and Thomas steelmaking processes, they could not have imagined that they would initiate a revolution in steel manufacturing with the development of the Linz-Donawitz (LD) converter – also known as the Basic Oxygen Furnace (BOF). Today, around 70% of global steel production is based on this technology. More than 200 LD (BOF) plants – including numerous turnkey projects – have been planned, built, and commissioned by Primetals Technologies.
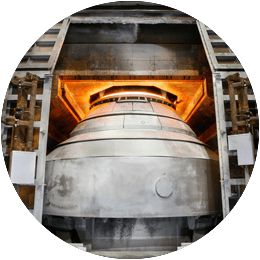
LD (BOF) plants from Primetals Technologies
In 1952 the Linz-Donawitz (LD) process – also known as BOF process – was developed in Austria and soon became the standard for iron ore based steelmaking. Starting from its invention the process was continuously optimized and improved regarding consumption figures, productivity as well as maintenance and is nowadays used successfully in steel plants all over the world.
Significant share of the developments and improvements for the LD process have been made by Primetals Technologies and its former companies. Nowadays Primetals Technologies is one of the leading solution providers for converter steelmaking with vast experience and wide reference base for completely new plants as well as for highly specialized and customized revamping and modernization projects.
Although the LD process is already a very mature process Primetals Technologies is continuously investing in developments for further improvements of the process and the equipment. Modern numerical simulation methods, process models, logistic simulations and full 3D modelling are some of the powerful tools used for this purpose.
Most recent trends in development are more accurate process control and process optimization by numerical models, increased level of automation to reduce manual workforce in hazardous areas and equipment optimization to increase lifetime. All these small steps together with our long term experience allow Primetals Technologies to be one step ahead of competitors and offer trendsetting solutions to our customers.
Special Converters
While for normal carbon steel production LD process is used in almost all integrated steel plants all over the world, special converters are used for high alloyed steels, processing of high rates of scrap and Direct-Reduced-Iron or processing of hot metal very high in Silicon content. Primetals Technologies has a wide portfolio of special converters; most important are bottom blowing converters that allow also for lime and coal injection as well as combined blowing converters. Characteristic for these converters is the bottom blowing with natural gas cooled tuyeres in the converter bottom and equipment for lime and coal injection. The bottom blowing leads to excellent mixing of the liquid bath, hence, all metallurgical reactions are close to their equilibrium. As a consequence yield of the process is higher compared to pure top blowing converter and process control is easier.
Primetals Technologies is the leading supplier for special converters and realized several references in the last years. Especially equipment and automation for the bottom blowing has been improved and optimized within the last years to fully comply with actual standards. One of the latest developments for special converters is the Jet Process. It combines a bottom blowing converter with a hot blast system. The hot blast blown from top ensures that the coal injected is fully combusted and almost all the heat is transferred to the liquid bath. As a result an overall efficiency of more than 50% is reached and a wide range of scrap rates can be processed in highly productive manner. A first reference for the Jet Process was realized recently with a customer in Asia.
Want to know more? Go to Integrated Plants & Solutions
Intelligent automation for steelmaking
State-of-the-art production of high-quality steel requires standardized and reproducible processes. Primetals Technologies process automation implements these requirements, consequently leading to improved hitting rates for carbon and temperature, lower flux material consumptions, higher Fe yields and optimized production times. Dynamic production control is assured by application of Steel Expert, a comprehensive suite of metallurgical process models.
Our process models optimize and control the steelmaking process during the entire treatment in BOF converter plants, based on flexible production schemes depending on the target steel grade.
The precalculation model - Steel Expert Prediction – simulates the whole BOF process before and after scrap and hot metal are charged. It determines the optimum blowing and stirring strategy, as well as the addition of flux and tapping alloying materials. During the blowing process Steel Expert Supervision cyclically calculates the ongoing reactions in the steel bath and in the slag. If a sublance is available, the Inblow model determines corrective actions based on the measured values, in order to achieve the required carbon and steel bath temperature. If a continuous offgas measurement (e.g. Lomas) is available, the Dynacon model is applied for dynamic blow end detection. Based on the actual offgas data Dynacon calculates the carbon content of the steel bath and suggests the optimum time for blowing stop.
Further highlighted technological packages:
- Lomas: fully automated continuous offgas measurement and analyzing
- BOF Tapping Expert: automatic, reproducible, standardized and safe steel tapping
- Equipment Position Monitor: automatic electronic tracking of metallurgical vessels at treatment stations
ECO Solutions for converter carbon steelmaking — Saving resources, creating value
Please follow the corresponding links to learn more about our competences.
Gas Cleaning
Energy Efficiency
By-Product Recycling
Water Treatment
ECO Consulting
TECHNOLOGY AND MODERNIZATION PACKAGES
Get striking results with incremental investments
Name | Short Description |
---|---|
Scrap Torch Cutting Machine | Environmentally clean scrap processing |
Scrap Type Monitor | Fully automated solution to identify and classify scrap on a yard |
Scrap Loading Controller | Automation supported scrap loading from yard to scrap buckets/chutes |
Scrap Profile Monitor | Fully automated 3D profile and volume measurement system for scrap piles |
Scrap Composition Monitor | Automatic identification of unwanted or dangerous ingredients in the scrap |
Bag Break Monitor | Bag break detection and localization for pulse jet bag filter-plants |
Freeboard Monitor | Online measurement system for ladle freeboard during tapping |
Bag Cleaning Monitor | Acoustic monitoring of pulse jet bag filter plants |
Discharge Monitor | Acoustic monitoring of truck or wagon discharging |
Material Type Monitor | Automatic identification of the type of material on conveyor belts |
Grain Size Monitor | Acoustic measurement of material grain size on conveyor belts |
Equipment Position Monitor | Reliable identification and tracking of metallurgical equipment throughout the steel plant |
Automatic Gas Coupling | Automatic gas coupling for ladle stirring |
BOF Tapping Expert | Safe tapping for all types of steelmaking converters - LD (BOF), AOD and KOBM |
Bag Filter Controller | Smart control of bag filter cleaning for dedusting plants |
BOF Optimizer | Dynamic process optimization (Level 2) for LD (BOF) Steelmaking |
Leakage Monitor | Leakage detection system for water cooling circuits |
Lance Checker | Test and diagnosis system for liquid iron and steel measuring devices |
LiquiRob for Steelmaking | Robotic solution for EAF, BOF, ladle furnace, VD |
LF / RH /VD Optimizer | Dynamic Process Optimization (Level 2) for Secondary Metallurgy (LF/RH/VD) |
Lomas | Gas analysis system for very hot corrosive and dust-loaded process gases |
SlagMon | Reliable slag detection for optimized tapping |
Vaicon Drive Damper | Vibration damping system for AOD and bottom blowing converters |
Vaicon Measuring Manipulator | Measuring and sampling at tilted LD (BOF) converter |
Vaicon Stopper | Pneumatic slag retention system for LD (BOF) converters |
Vaicon Sublance 2.0 | Vertical sublance for converter measurements |
Vaicon Stirring | Bottom stirring for LD (BOF) converters |
Name | Short Description |
---|
Name | Short Description |
---|
Name | Short Description |
---|
Name | Short Description |
---|
Name | Short Description |
---|