ALUMINUM COLD ROLLING MILL — HIGH-PRECISION MILL FOR BREAKDOWN & FINISHING
Primetals Technologies' aluminum cold rolling mills offer a blend of innovative design and proven technology for both new and revamp projects.
From transport to construction, from packaging to automotive, each end market for flat rolled aluminum comes with its own set of production challenges. Primetals Technologies' aluminum portfolio provides you with the optimum equipment, correct mill setup, and control systems crucial to meeting exacting quality requirements. Our online modelling solutions feature fully integrated process control, automation and drive systems, delivering exceptional rolling results and enabling tight tolerance strip production with maximum yield.
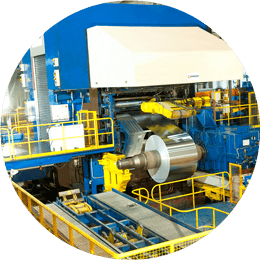
Aluminum Cold Rolling Mills — Solutions for high-precision rolling
Primetals Technologies' cold mill portfolio comprises:
- Breakdown mills
- Thin-strip mills
- Tandem mills (two, three, and four-stand)
Offering both 4-high and 6-high mills stand designs, we can provide an extensive range of proven technologies for greenfield sites and modernizations of existing mills that can be tailored to meet your particular rolling needs. Our online process models connect to our fully integrated process control and automation drive system to optimize the rolling process for you.
Performance actuators offered with our mills improve mill production, coil yield, strip flatness, and quality. These include:
- Universal Crown Control Mill (UC-MILL) for excellent strip flatness and surface quality
- Integral Solenoid Valve (ISV) spray system for improved profile and flatness control
- Induction heating maximises coil yield and eliminates flatness errors
- Short coil handling time increases mill availability
- Edge wipe unit which removes edge beads to improve strip dryness
- Interstand cooling for tandem mill solutions increases rolling speed
- Schneider Coolant Filtration maximises mill availability and minimizes waste
- Heavy-duty Air Bearing ShapeMeter (ABSM) roll provides a highly sensitive solution for accurate flatness feedback
- Vapor Shield fume cleaning and rolling oil recovery reduces harmful emissions, thereby improving your environmental credentials
Want to know more? Go to Lifecycle Services & Integrated Plants & Solutions
Complete automation and process control for Aluminum Cold Rolling Mills
Plant productivity and product quality are governed to a large extent by the quality of plant automation, process control, and available process optimization functions.
- Digitalization packages (e.g. TPO, MAT, Condition Monitoring, Intelligent Sensors)
- Production management systems (Level 3)
- Physical models combined with artificial intelligence (Level 2)
- Automation solutions, including advanced technological controls (Level 1)
For existing installations optimization packages are available as standalone solutions designed to improve production efficiency and strip quality.
Throughput maximization with:
- Production Optimization Modes
- Mill Set-Up System (MSU) as alternative to a model-based Level 2 system, including user-friendly pass schedule strorage and mathematical calculations
Excellent strip quality with:
- Automatic Gauge Control (AGC)
- Flatness Expert - Model-based Automatic Flatness control
- Roll Eccentricity Expert for uniform and accurate strip thickness
- Coil Eccentricity Expert for uniform and accurate strip thickness
Our solutions encompass:
- Process Automation Twin for safely developing new materials and optimizing rolling schedules
- Central Operation Cockpit to support mill operation (centralized operation)
- Software architecture open for customers' own future developments
- Modular structure for step-by-step modernizations
TECHNOLOGY AND MODERNIZATION PACKAGES
Get striking results with incremental investments
Name | Short Description |
---|
Name | Short Description |
---|
Name | Short Description |
---|---|
Flatness Expert | Flatness control for tight shape tolerances |
ALU TCS | Compact and integrated technological control system for single cold rolling mills |
Integrated Solenoid Valve (ISV) Spray System | ISV Roll coolant spray bars for hot and cold rolling mill strip flatness control |
Position Transducer | Position measurement of rolling mill hydraulic capsule |
Hot Edge Sprays | Applying hot coolant to work rolls for tight edge correction |
Edge Wipe | Removal of roll coolant from strip edge |
Beverage Can-Line Filtration system | Filtration of coolant during bodymaking of beverage cans |
Schneider® Filter | Coolant Filtration System for rolling mills |
Air Bearing Shapemeter | Shape measurement of rolled metal sheet and foil |
Modular Coil Shuttle System (MCS) | Rail-based, fully automated modular coil transport system |
Induction Heater for Work Rolls | Induction heating for work rolls for effictive edge-tight control |
EdgeMon | Inspection of side-trimmed strip edge surface for steel pickling and processing lines and aluminum rolling |
TorqueMon | Inline measurement of roll spindle torque for rolling mills |
Roll Eccentricity Expert | Elimination of a known strip thickness quality disturbance from rolls |
Reference Story: Advanced Aluminum Cold Rolling Mill
Customer:
C. S. Aluminium Corporation, Taiwan
Type of Plant:
Non-Reversing Single Stand Cold Mill
Technical Data:
Material: 1xxx~6xxx series
Product thickness: min.0.1 mm
Width range: 1,000mm~2,150 mm
Max Rolling Speed: 2,000 m/min
Our Solution:
The application of the Universal Cold Mill (UCM) principle and coolant spray zone control delivered excellent shape control, and made high-speed rolling of thin gauge possible.